To demonstrate the usefulness of the technique [aligned nanowires using bubbles], the researchers transferred the films to silicon wafers, then used conventional techniques to deposit electronic contacts on the films. The nanowires bridged the contacts, serving as semiconducting channels for working transistors.
Lieber says that early applications could include accurate home tests for illnesses such as cancer, influenza, and sexually transmitted diseases. In such a device, a protein biomarker for prostate cancer, for example, would connect to the nanowires, changing the wires’ conductivity and registering the protein’s presence. Nanowires provide three-orders-of-magnitude-greater sensitivity than current tests, Lieber says. And because the nanowires directly detect the proteins by generating an electronic signal, such tests would provide results right away, making it unnecessary for researchers to wait for results to come back from the lab. What’s more, tests for multiple biomarkers can easily be combined on a chip. An array of hundreds of nanowires, each chemically modified to react with a specific protein, could be used to create a highly accurate cancer test.
The nanowires could also be used in flexible displays to turn pixels on and off. Conventional high-speed transistors require fabrication temperatures that would melt the plastic substrates used in flexible displays. But nanowires can provide the same performance without the need for high temperatures.
The researchers are now studying the process to find ways of packing the nanowires closer together, which could allow for applications beyond those for sensors and displays, such as for memory. Before the process can be used for manufacturing, though, it will need to be automated, possibly in ways similar to the blown-bubble techniques now used for high-volume production of plastic bags. Lieber says that the method could be used in nanodevice manufacturing within one to two years.
The new technique involves blowing bubbles made of an epoxy polymer mixed with either nanowires or carbon nanotubes. The researchers pour the mixture onto a circular surface equipped with a small hole; the polymer-nanowire mixture forms a membrane over the surface. The researchers then force nitrogen gas through the hole, expanding the membrane until it forms a bubble about 25 centimeters wide and 50 centimeters tall. A metal ring stabilizes the bubble as it grows, with the polymer material stretching to become a 200-to-500-nanometer-thick film containing evenly spaced nanowires or carbon nanotubes lined up and facing in approximately the same direction. The researchers speculate that sheer forces caused by the growth of the bubble make the nanowires line up.
The resulting film can be transferred to a number of surfaces, including silicon and flexible plastic. To do this, the researchers position silicon wafers or other materials so that when the bubble inflates, the surface of the bubble presses against them.
Nanowerk also has information on the process
In the present process, relatively low concentrations of CNTs and nanowires, less than 1%, are dispersed in the polymer suspension. As a result, the distance between individual nanostructures is relatively large (greater than 2 µm). “You need at least 4-5% by weight to get a good mechanical structure, but this is quite achievable, for example using surfactants or alternative polymers. There should now be real advances made quickly by learning from other areas” says Lieber.
Generally, this technique would allow fabrication of large-area thin film products with all types of nanoscale components. The bubble films could be further processed to make arrays of nanoelectronic or optical devices, sensors, and field emitters for flat panel displays. Bubble films coated on plastic substrates could be fabricated into flexible micro/nano systems. Introducing nanomaterials could also produce reinforced plastic films with better mechanical properties. The regular alignment of CNTs within the film would give it high tensile strength, potentially higher than Kevlar, and would make this an intriguing material for many materials applications, from airplane wings to protective clothing and armor.
Cao says that the team is now exploring several areas, including fabrication of nanosystems with distinct electrical or optical properties, and use of different polymers to facilitate subsequent device fabrication. “For example, we have developed photopolymer (PMMA) based bubbles that can be directly integrated into modern microfabrication technique to pattern electrodes.”
He also cautions that there are challenges facing their research in the near future: “A better understanding of the mechanism of nanostructure alignment during bubble blowing process is necessary for further optimizing the process, and materials and instrumentation need to be developed for large scale production.”
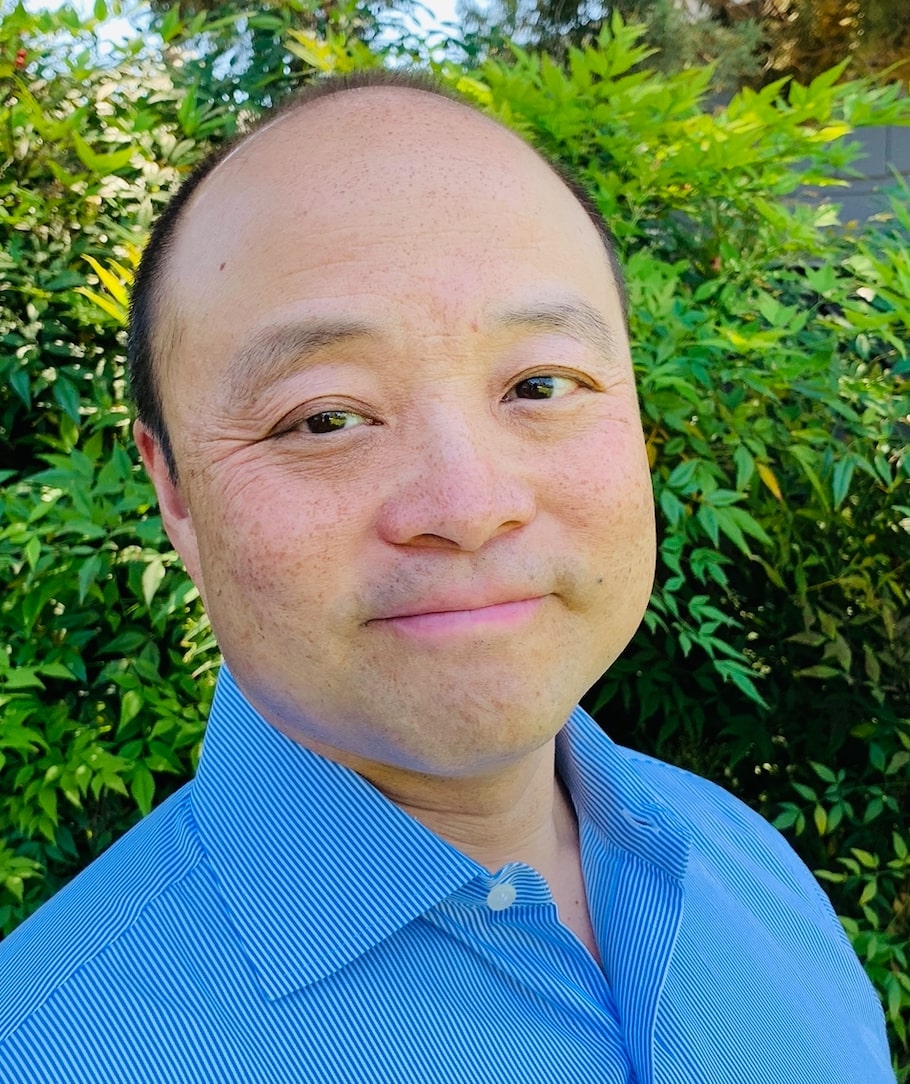
Brian Wang is a Futurist Thought Leader and a popular Science blogger with 1 million readers per month. His blog Nextbigfuture.com is ranked #1 Science News Blog. It covers many disruptive technology and trends including Space, Robotics, Artificial Intelligence, Medicine, Anti-aging Biotechnology, and Nanotechnology.
Known for identifying cutting edge technologies, he is currently a Co-Founder of a startup and fundraiser for high potential early-stage companies. He is the Head of Research for Allocations for deep technology investments and an Angel Investor at Space Angels.
A frequent speaker at corporations, he has been a TEDx speaker, a Singularity University speaker and guest at numerous interviews for radio and podcasts. He is open to public speaking and advising engagements.